The challenges for business owners who rely on imported goods, continues into 2021 as the the cost of bringing goods in from overseas continues to increase after reaching record highs in December, as various market forces exacerbated by a combination of the global Covid-19 pandemic coupled with Brexit impact on both product lead times and the retail prices for goods imported from overseas. In my latest article I look at what is causing these issues, the impact on McAra and our customers.
Raw material increases
The cost of production has increased for most Asian manufacturers because of higher input costs, particularly raw materials such as cardboard, paper and plastics. These price hikes are partly a result of higher fixed costs, lower capacity utilisation and overheads such as expenses related to covid safety protocols
A good example of this is the price of cardboard. Since the start of the Covid-19 pandemic in March 2020, use of cardboard boxes has soared led mainly by delivery services including Amazon as well as the health sector.
With the high street and physical retail remaining closed for much of 2020 and into 2021, consumers have turned to online shopping in their droves with a huge increase in the numbers of consumers making purchases online.
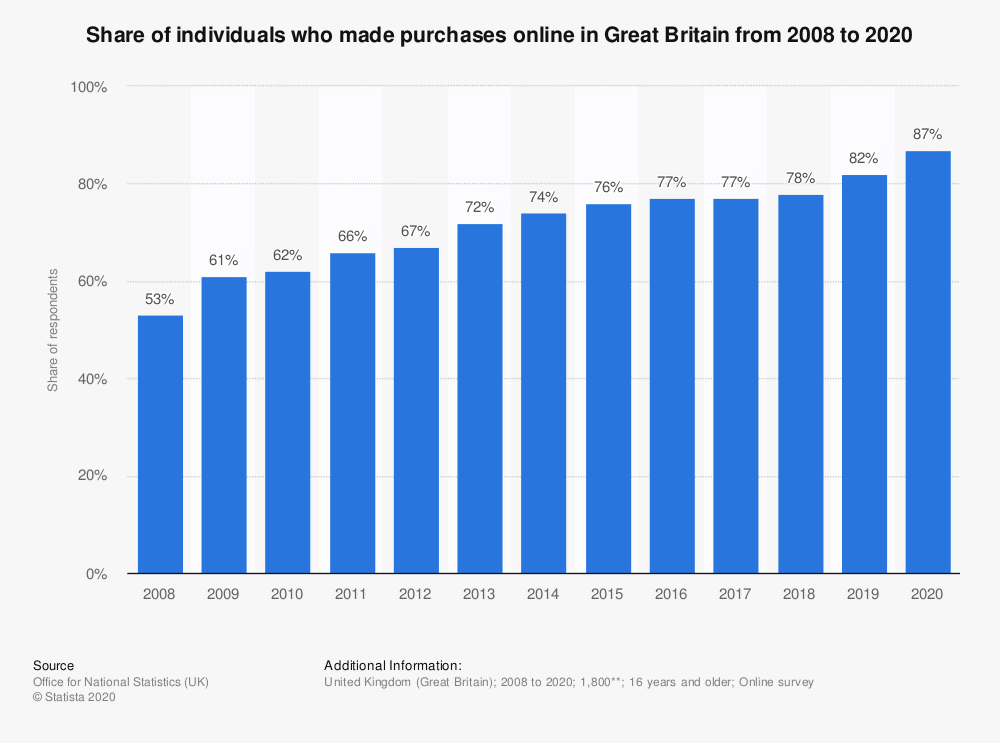
This change in consumer habits has in turn increased demand for the cardboard used in the packaging of goods for delivery in customers, creating shortages and increasing the price of the commodity.
Similarly, prices for paper products are up in China due to rising cost of raw materials during the pandemic and stricter environmental protection rules. A large amount of raw materials used in paper production in China is imported from overseas, with the logistics cost of imported raw materials increasing which has led to the price rises.
The demand for plastics has also increased the cost of this raw material with example price increases of between 20% (for Tapes) to up to 40% for office equipment since Autumn 2020.
In turn, the increased production of personal protective equipment (PPE) has caused a shortage in rubber, which is used to manufacture medical gloves. When this combined with poor weather in Thailand (where much of the world’s rubber is sourced) this has increased the cost of this raw material significantly.
We fully expect little change in raw material costs in 2021 as the world’s manufacturing hubs and global supply chain return back to normal production levels during the year, which will create unpredictability and volatility in pricing over the next twelve months.
Challenges of the Global Supply Chain
Global supply chains have been disrupted with freight costs increasing by up to four times pre-pandemic levels, as demand for goods starts to increase as the world emerges from the Covid-19, supported by the increase in online purchases by consumers during lockdown.
Since October 2020 we have seen significant and unprecedented increases in the freight costs of importing goods from China. As we write this article rates are at levels never seen before due to a combination of factors, including a reduction in shipping services into the UK, shortages on shipping containers in China and delays in UK ports caused by pandemic related staff shortages.
According to the Financial Times a 40ft container from China to northern Europe that might have cost $1,500 (£1,100) six weeks ago was quoted at £9,000, with the price of a 20ft container has risen from $800 in the summer to over $3,000 now.
As reported in The Guardian Covid-19 disruption has resulted in many of the worlds largest shipping lines avoiding UK ports, with vessels from Asia sailing to other European ports such as Rotterdam, Zeebrugge or Hamburg. Goods on these vessels destined for the UK therefore find space on vessels that are planning to visit UK ports which due to demand shipping lines are charging record prices
With increases also affecting the costs of European road freight, and combined with the additional challenges of new Brexit import tariffs for goods that have a country of origin outside of the EU.
According to Gavin van Marle in The Loadstar, the impact of Brexit on the European road freight market has been immediate showing a Europe-wide decline in capacity of some 16.4% in November and 16% year on year. This was led by huge capacity decreases on routes to and from the UK, which has subsequently pushed up road freight rates.
In addition, UK ports are short handed due to staff shortages, causing congestion and delays with empty containers being left stranded. Pre-pandemic it would typically take around two to three days to return an empty container back to port after delivering the imported goods to the retailer, before beginning its journey back to its original location. The impact of Covid means many ports are working with skeleton staff, and under Covid 19 working protocols, which is delaying the turnaround time for inbound containers from three days to nearly three weeks in some cases.
This in turn has created issues in Asian ports where shippers are struggling to find enough empty containers to export their goods to Europe, creating a real imbalance. This has impacted on container freight prices (S&P Global Platts Index) driving them up beyond $10,000 which will result in higher prices for goods as retailers have to pass these costs onto the consumer.
The impact for consumers
The result for consumers and the end users of products is price rises as manufacturers, distributors and retailers have to pass these costs on to their customers (BBC).
As you can imagine these economic factors are having a huge impact on the McAra business. Whilst we always try to avoid passing on supply chain increases to our customers the current levels of increases and the forecasts for the remainder of the year present a challenging picture for consumers as prices will rise for many imported products.
So whilst optimism remains amongst manufacturers as the recovery starts in the UK, many are reaching the point where increases to their overheads are beginning to be passed on to their customers.
Why are firms having to increase their prices? Why can’t they just absorb the costs in their profits? This is a question that many consumers will be asking themselves as they face these increased costs of everyday goods.
What can you do to mitigate these increases?
With the current costs and availability of cardboard and other raw materials, it’s a good idea to review where you use this material within your business and see if you can reduce usage or replace it with another material. For instance, can you reduce the amount of cardboard used, by using smaller boxes package goods, or can you even find a completely different way of packaging your products using other materials?
Working closely with your suppliers and other parts of the supply chain to plan your recovery. Keeping your key suppliers abreast of your future planning and forecasts will ensure they can be clear around your expectations and demand for products in the future. Working in partnership with your supply chain any potential risks to supply through the availability of raw materials or freight issues will be identified and factored into your planning and financial forecasting, hopefully removing any surprises later down the line.
As the world recovers from the global pandemic over the next 24 months we will still face challenges as the world’s manufacturing and supply chains start to normalise to the post pandemic world. I would be really interested to get your feedback on how your business is managing your supply chain and freight price increases. If you are a supplier, how are you managing this with your customers? Please add your comments to the below or send me a message. It would be great to connect and share ideas.